I was just born in North Bend, Washington, but where did I really come from? These guys designed me, but many more people helped bring me to life. I’m proud of my Washington roots, 95 percent of my parts are made by suppliers around the Puget Sound and the Greater Northwest. Here is my story:
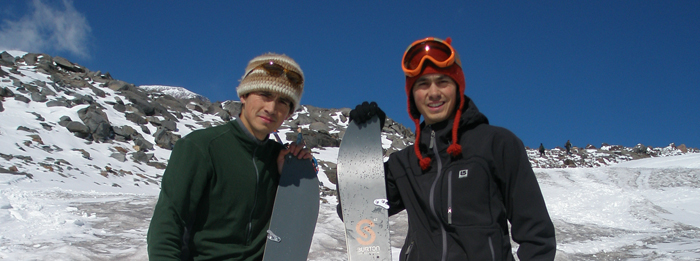
Bryce and Tyler, creators of Karakoram
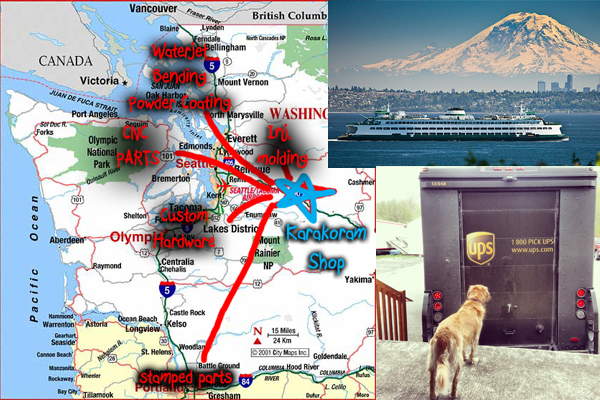
Washington supply chain, ferry across Puget Sound, and Cedar waiting for Patrick (our UPS guy)
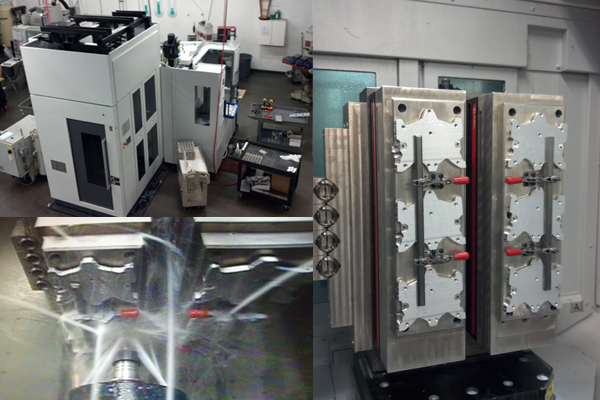
Horizontal Mill cutting heelstays
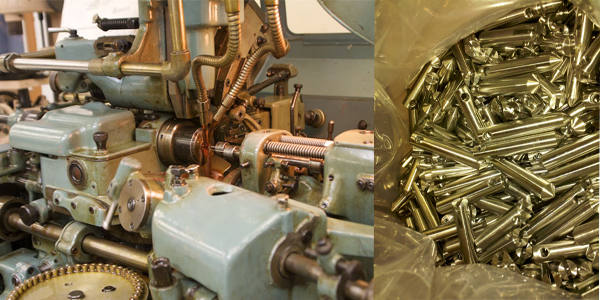
Screw machine turning and milling pins
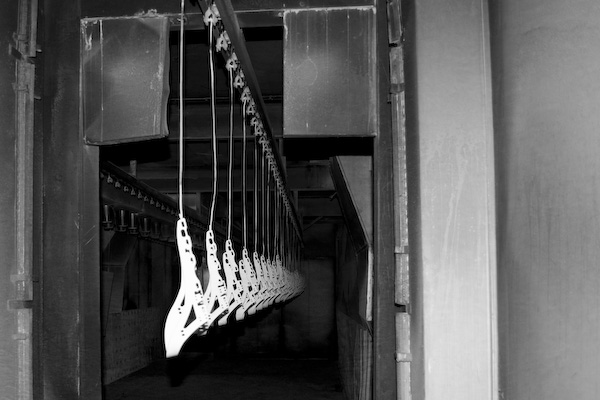
Heelcups travelling through a powder coating oven
Parts are meticulously assembled into the heelstay and riveted closed. Each lever is checked for the perfect over-center snap.[br]
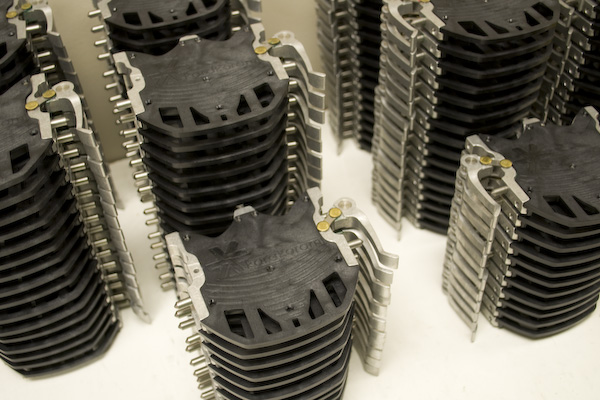
Stacks of heelstays ready for rivets
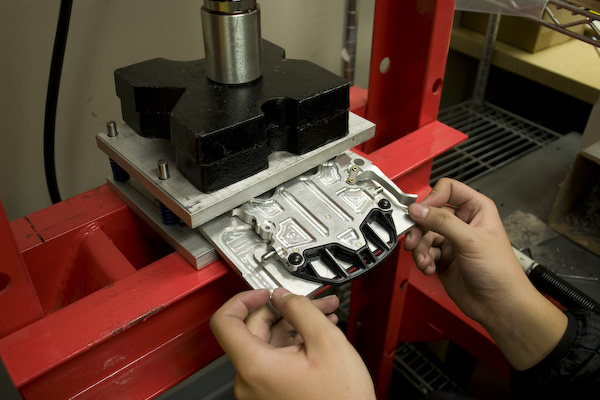
Final pressing of rivets on heelstays
![IMG_20130620_140043[1]](https://www.splitboardbindings.com/wp-content/uploads/2013/06/IMG_20130620_1400431-1024x1024.jpg)
Russell has a banana peel on his head
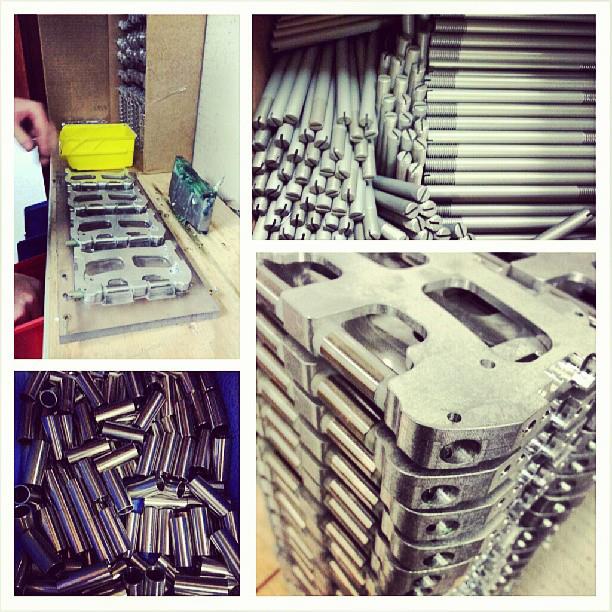
Toestay assembly
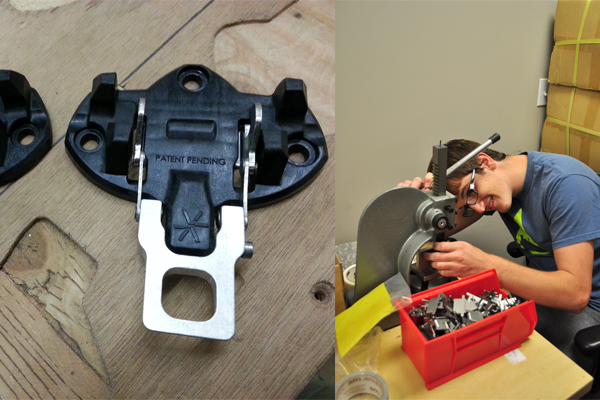
Riveting tour modes
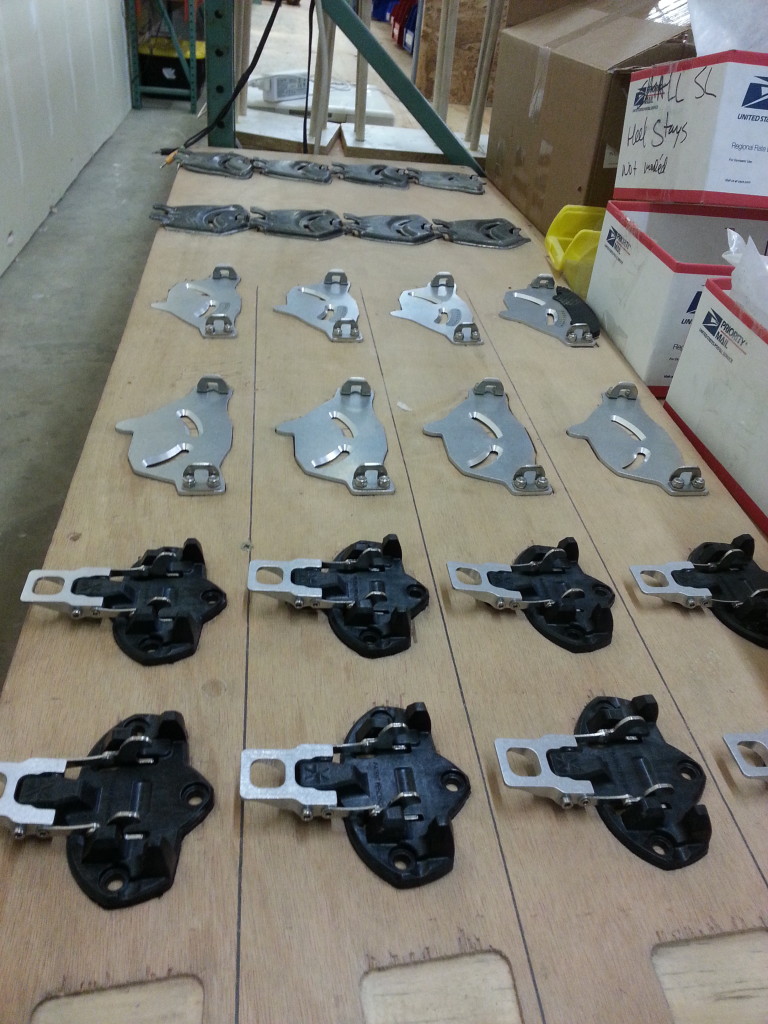
Layout table for packing
Now the exciting part begins, final assembly! Zip, zip, zip. An assembly fixture holds parts in place as a skilled binding technician (Russell, Robert, Tyler, or Bryce) torques screws to hold me together. I’m slid down the assembly line and my anticipation builds, one more step before I’m ready for snow. [br]
Robert assembles a Split30 Splitboard Binding[br]
Once finally assembled my builder runs me through a fit check jig and then puts me in a box to wait for a partner to climb and shred mountains with. [br]
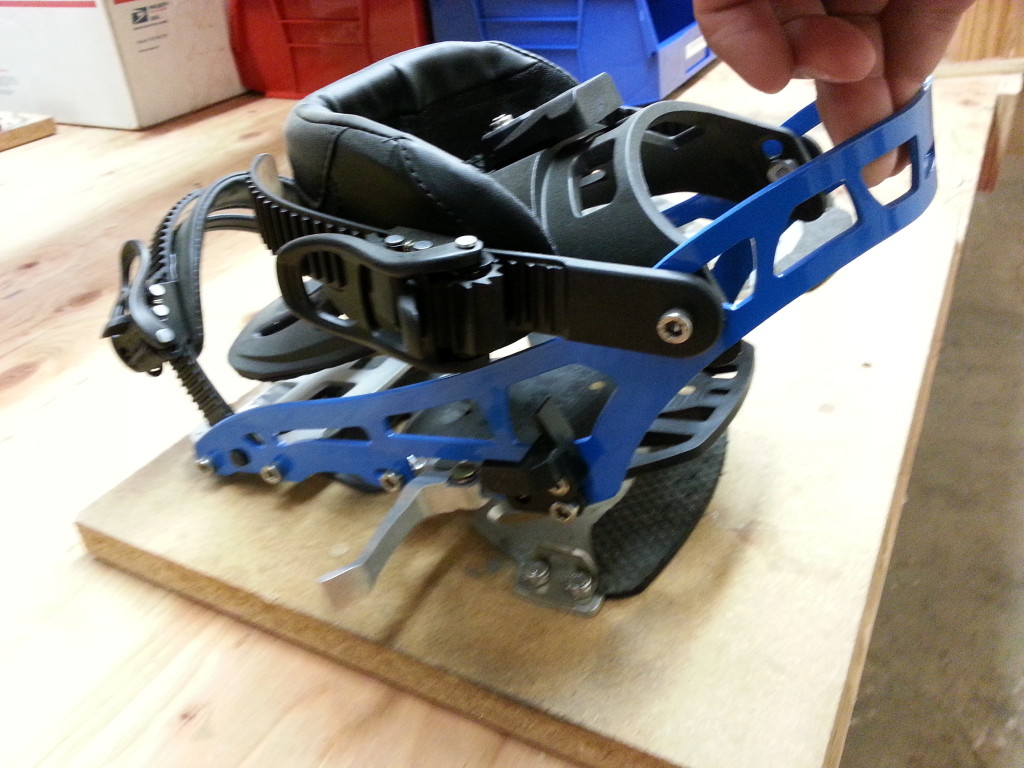
Test fitting binding on fixture
I could be your bindings, but I’m actually going to Jeremy Jones! Alaska, Europe, Japan, the Arctic adventures here I come! I’m manufactured and assembled in the USA, built for your adventures.[br]
Where will you take me? I’m particularly fond of long walks in the mountains…
It’s great to see how the best-designed splitboarding bindings in the world are made: right here in the NW! Great design, cutting edge materials, employing actual riders, and innovating every season–you guys are doing it right! Thanks!